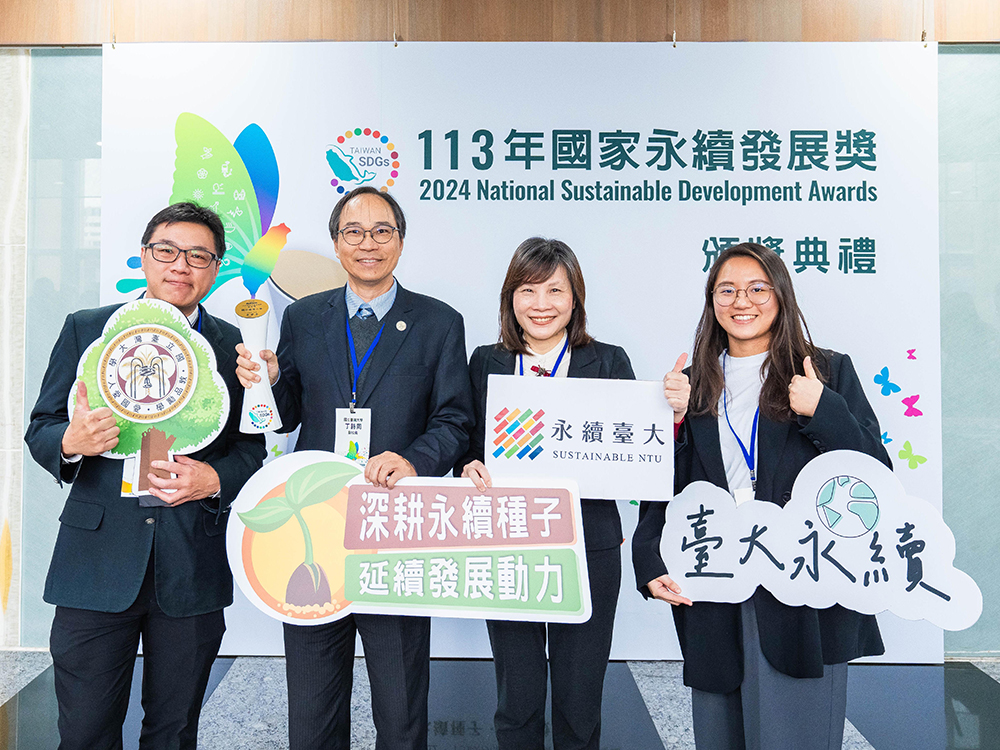
NTU wins the 2024 “National Sustainable Development Awards” for exerting influence in higher education
瀏覽器版本過舊,或未開啟 javascript
請更新瀏覽器或啟用 javascript
Spotlights
NTU team members, Guan-Ju Cheng and Prof. Hung-Wei Yen, at the Scanning Electron Microscope Lab
Figure 1. Tensile properties of D&P steel compared with other high strength steels, including maraging steel, nanotwinned (NT) steel, UFG-Duplex steel, TRIP/TWIP M-Mn steel, quenching and partitioning (Q&P980) steel, and dual-phase (DP780) steel.
Figure 2. Electron micrographs showing the complexity of nano/microstructure in the D&P steel (Results of the current artwork were all done at NTU).
Automotive, aerospace, and energy applications require metallic materials with ultra-high strength. Unfortunately, increasing strength often leads to the decrease in ductility, which is known as the strength-ductility trade-off. This creates a boundary for the applications of structural materials. For example, given their high hardness and ultra-high strength, ceramics and amorphous materials have negligible ductility. To simultaneously increase both the strength and ductility of metallic materials using conventional industrial processing routes is of great scientific and technological importance. However, this goal remains challenging for materials science researchers. Specifically, it is very difficult to improve the ductility of metallic materials when their yield strength is beyond 2 Gigapascal (GPa). Steels have been the most widely used metallic materials in human history and have achieved much higher industrial production efficiency than other metallic materials. Therefore, developing a strong and ductile breakthrough steel has been a long quest since the beginning of Iron Age. Excitingly, an engineering team comprising members from Hong Kong, China, and Taiwan has succeeded in developing a breakthrough steel that achieves high ductility at the yield strength of 2 GPa.
In addition to the substantial improvement of tensile properties, this breakthrough steel has achieved the unprecedented yield strength of 2.2 GPa and uniform elongation of 16%. This breakthrough steel has two advantages. The first advantage is low raw materials cost. The chemical composition of the developed breakthrough steel belongs to the system of medium manganese (Mn) steel, containing the Iron (Fe)-10%Mn-0.47%Carbon (C)-2%Aluminium (Al)-0.7%Vanadium (V) (mass percent). All of these elements have been widely used in the commercialized steels. The second advantage is that this steel is developed by using conventional industrial processing routes including warm rolling, cold rolling, and annealing. This differs from the development of some metallic materials where the fabrication process involves complex routes. Therefore, it is expected that the developed breakthrough steel has a great potential in hundred-ton industrial mass production.
Compared with the widely used automotive steels (see DP780 and Q&P980 in Figure 1) as well as the steel used in aerospace and defence (maraging steel), the newly-developed D&P steel demonstrated a higher yield strength while maintaining a better ductility (uniform elongation). The latest D&P steel also outperformed the NT steel developed by Prof. Huang in 2015, UFG-Duplex steel by Prof. Yen in 2015, and TRIP/TWIP M-Mn steel by Prof. Lou in 2016. In addition, the developed D&P steel demonstrated the best combination of yield strength and uniform elongation among all existing high strength metallic materials. In particular, the uniform elongation of the developed D&P steel is much better than that of metallic materials with yield strength beyond 2.0 GPa (see Figure 1).
The development of this breakthrough steel is a successful example of collaboration of young scientists from different regions in Greater China (i.e., Hong Kong, China, and Taiwan). The team led by Prof. Mingxin Huang (黃明欣) from the Department of Mechanical Engineering of the University of Hong Kong (HKU) is dedicated to studying the deformation mechanism of ultra-high strength metallic materials. In the research, Prof. Huang’s team firstly proposed a new deformation mechanism in which high dislocation density can improve both strength and ductility simultaneously. It is worth mentioning that a general belief in textbooks is that increasing dislocation density will elevate the strength but undesirably deteriorate the ductility. The team led by Prof. Haiwen Luo (羅海文) from the University of Science and Technology Beijing (USTB) is specialized in steel processing and has successfully produced high mobile dislocation density in this breakthrough steel. Prof. Hung-Wei Yen (顏鴻威) and Guan-Ju Cheng (程冠儒) from National Taiwan University (NTU) supported this new deformation mechanism by performing advanced microstructure characterization (see Figure 2). The research outcome is a collective contribution from young scientists in HKU, USTB, NTU, and the City University of Hong Kong. The study was published in the prestigious journal Science on 24 August 2017 with the title, “High Dislocation Density-Induced Large Ductility in Deformed and Partitioned Steels.”
(Source: Dr. Hung-Wei Yen, Assistant Professor of the Department of Materials Science and Engineering at National Taiwan University)
NTU wins the 2024 “National Sustainable Development Awards” for exerting influence in higher education
Prof. Chih-Kung Lee of NTU’s Institute of Applied Mechanics elected NAI Fellow
NTU Launches Startup Initiatives at Zhubei Campus
2024 NTU-KU-UHH Trilateral Symposium: Uniting for Sustainable Future and Next Generation
Signing Ceremony for the donation of “Next-Generation Smart 3D Geospatial Information Center” at NTU Zhubei Campus
Current Spotlights